Garneau Twin Towers
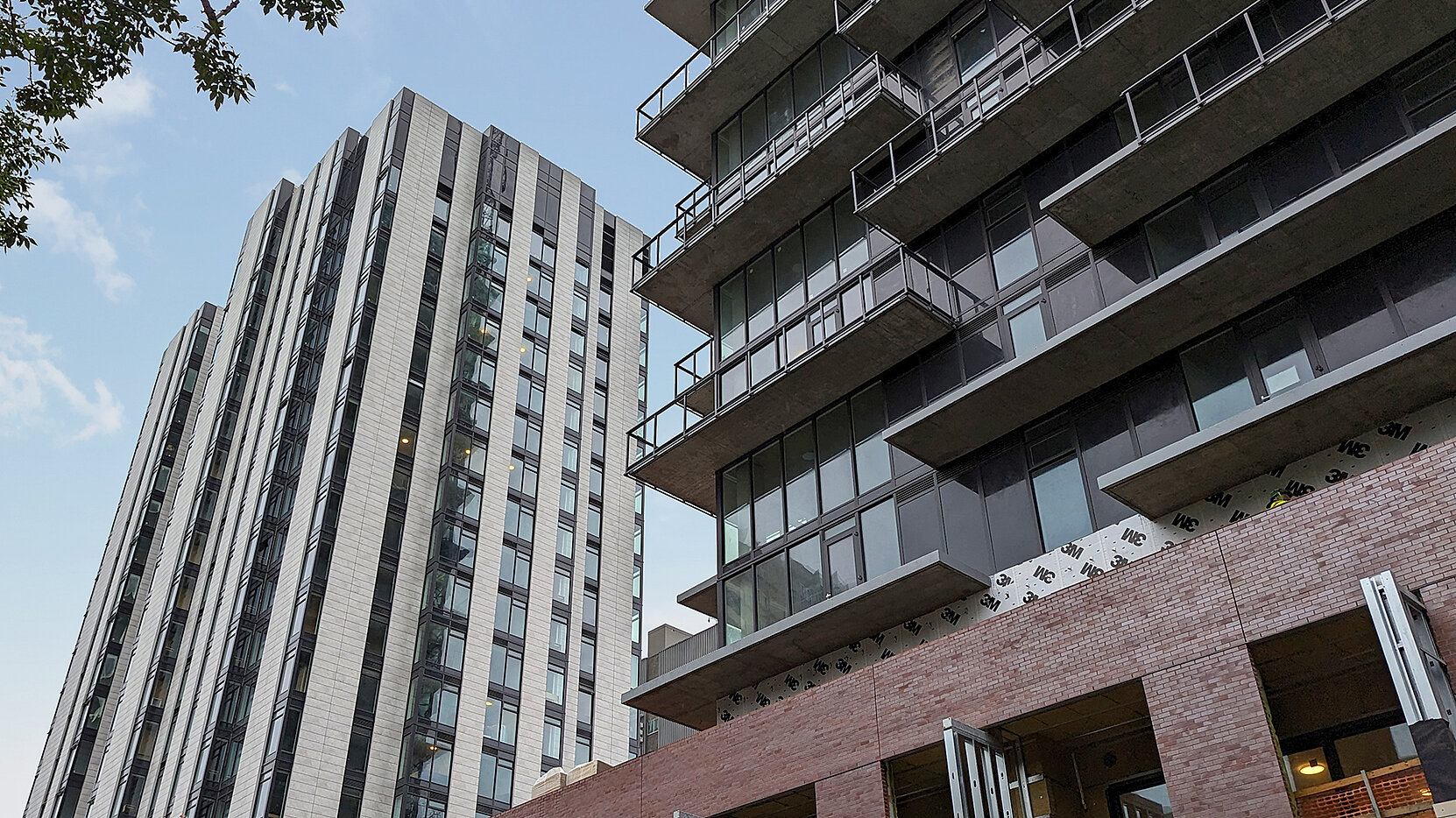
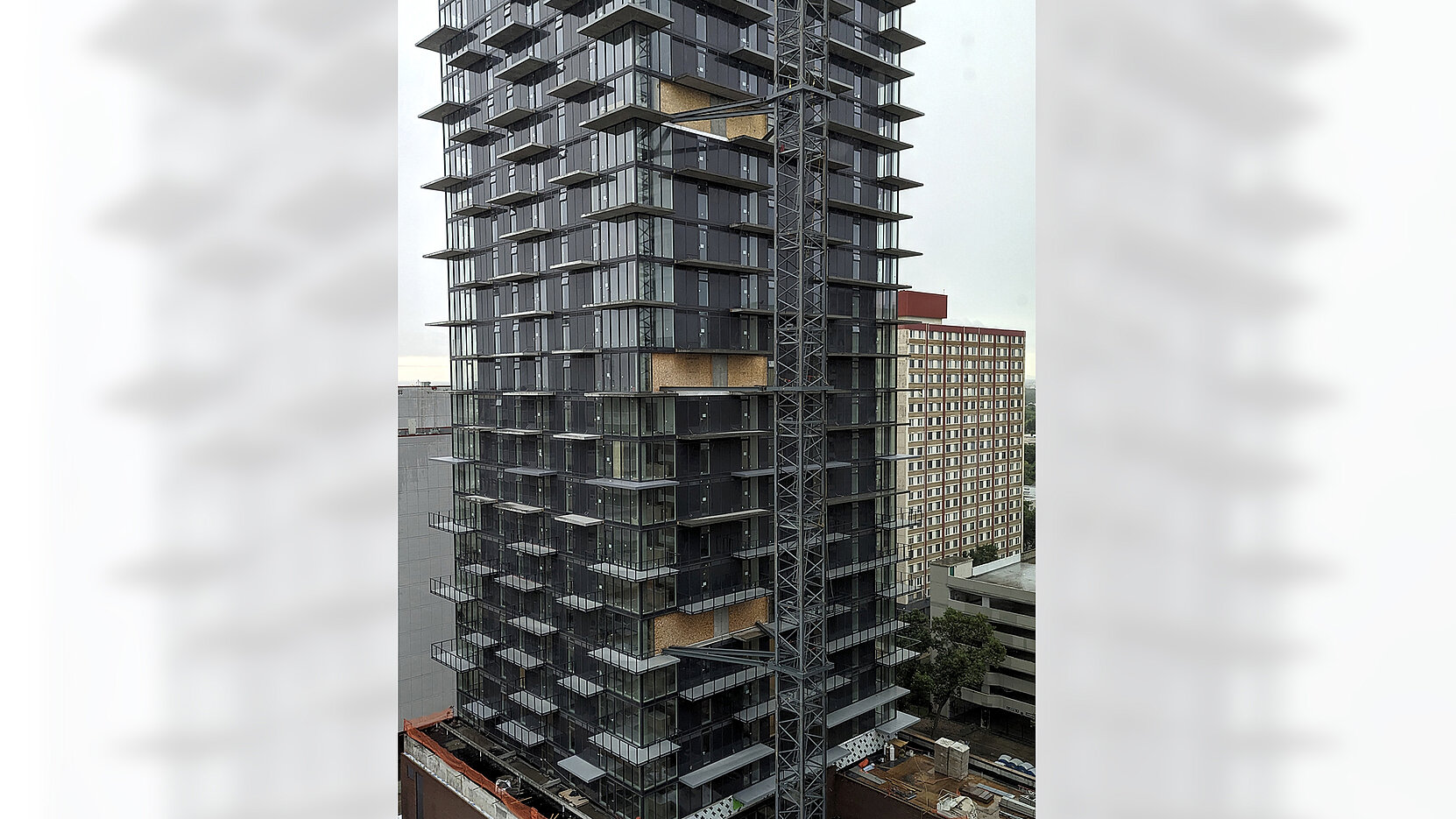
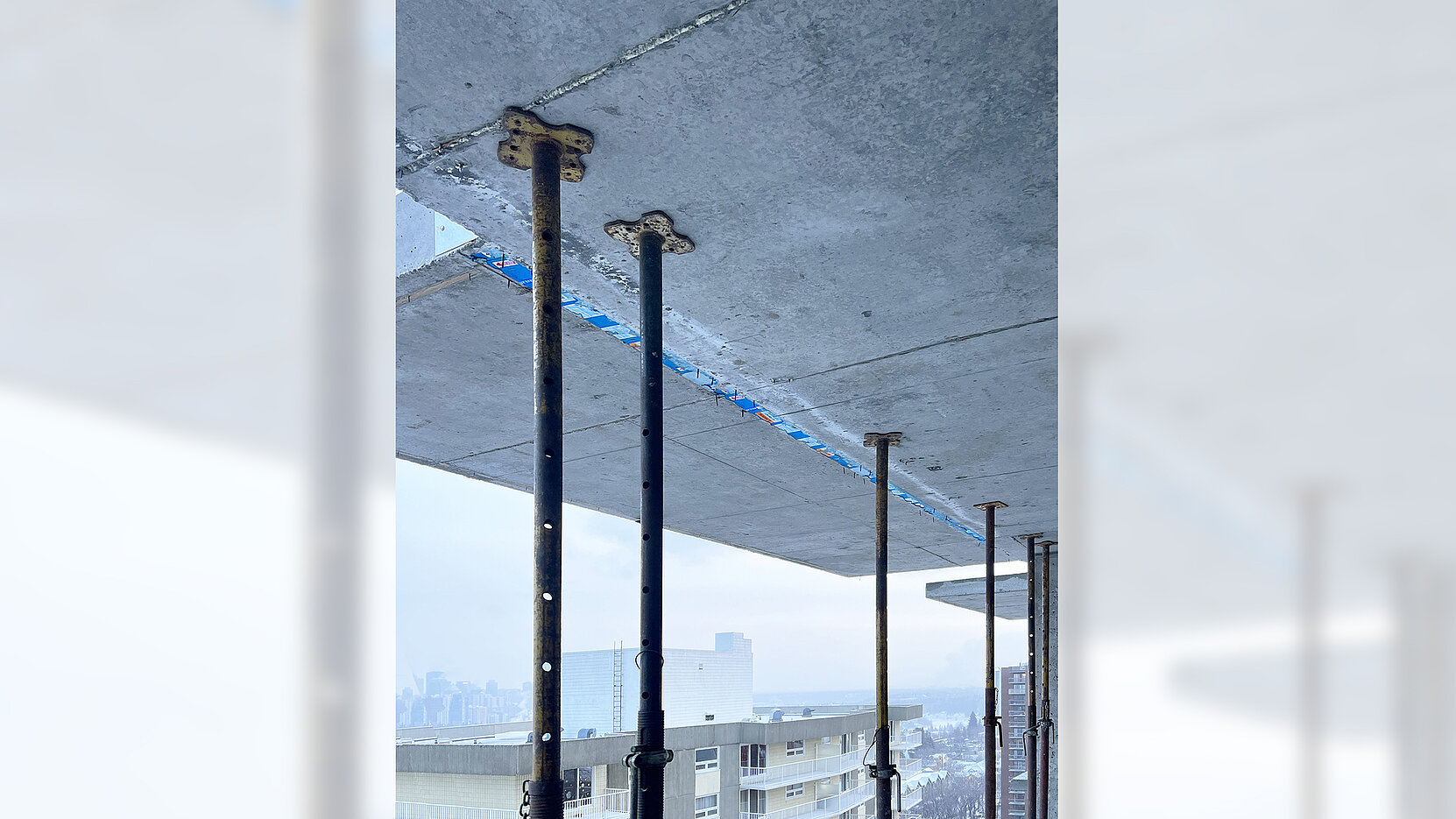
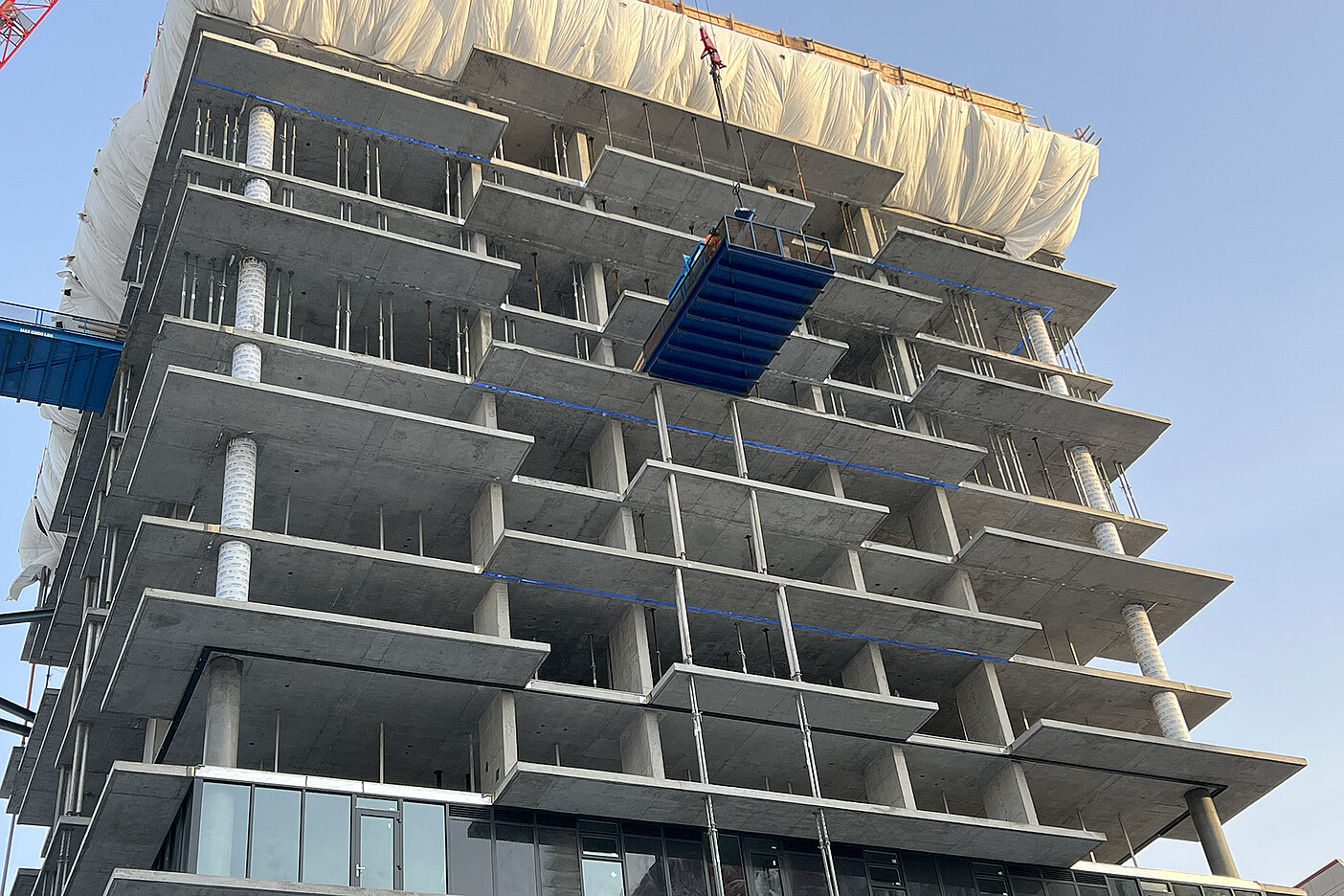
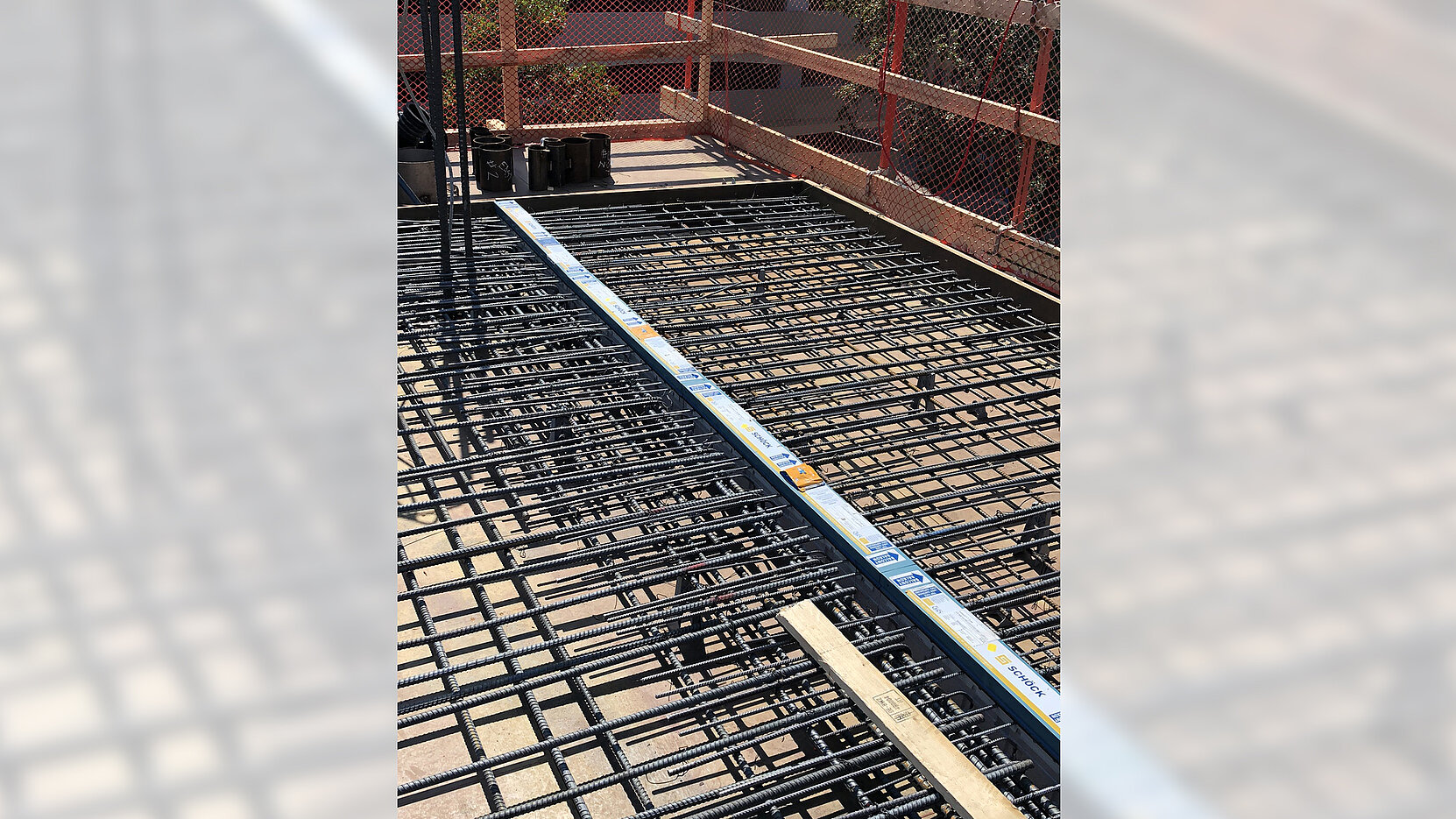
Project Highlights
- Student housing tower achieves 7.7% energy savings over the 2011 NECB
- Structural thermal breaks insulate The Eleanor's balconies, offering protection from the cold Edmonton winters
- “The energy model was pretty clear. If we don’t thermally break these balconies, we’re not going to meet the energy model requirements. It's a cost that delivers a real benefit,” said RDH Building Science Senior Project Engineer Alan Bowden. "."
- Project structural engineer, DIALOG’s Steven Oosterhof, notes, “Thermal breaks were proposed as a solution to thermal bridging and were carried through value engineering because of the value they bring. They are an excellent solution because they fully integrate into the structure."
Maclab's twin-tower complex in Edmonton's Garneau District blends high-end residential with efficient student housing
The Maclab Development Group recently completed and opened a $220 million twin-tower complex in the storied Garneau district (86th Avenue and 112th Street). Designed by Diamond Schmitt, The Laurent and The Eleanor, honoring two of the area’s first inhabitants, Laurent and Eleanor Garneau, comprise a 20-storey student residence and 30-storey market rental tower that sit atop a shared three-storey podium housing 12 single-family townhouses and 613 sq m (6,600 sq ft) of retail space.
Developer-owner Maclab views the complex as a long-term investment, opting to include desirable amenities and ensure that all units provide superior comfort and energy efficiency, including 260 high-rise residential units in The Eleanor that have code-required outdoor space (Edmonton Bylaw 15217 4.3iv) in the form of balconies (not included or required for the Laurent student housing).
Preventing heat loss through The Eleanor's balconies
The Eleanor offers 260 one-, two-, and four-bedroom residential high-rise units in addition to 12 single-family townhouses. According to the energy modeler Footprint, the project achieved a 7.7% energy savings over the 2011 National Energy Code of Canada for Buildings (NECB) through the use of structural thermal breaks at balconies and other energy-saving measures such as a high performance full-façade double-glazed window wall system, thermally-broken curtain wall on the ground floor and podium, in-suite energy recovery ventilators, variable-speed pumps, and high-efficiency natural gas condensing boilers and water heaters.
Each Eleanor apartment provides a cantilevered balcony, potentially creating a thermal weak point through the building envelope as a result of thermal bridging. The project team utilized structural thermal breaks to prevent balconies from dissipating heat energy into Edmonton’s cold climate. Unabated, thermal bridging leads to heat loss, occupant discomfort, and potential for condensation and mould growth on interior surfaces.
Building envelope consultant, RDH Building Science Senior Project Engineer Alan Bowden points out, “The total projected areas of the balconies are actually quite small, relatively, however their impact on heat transfer across the building envelope is quite large due to the conductive nature of reinforced concrete. The energy model was pretty clear. If we don’t thermally break these balconies, we’re not going to meet the energy model requirements.”
“The energy loss from balconies can be significant,” adds Diamond Schmitt Technical Director Rod Maas. Diamond Schmitt served as project architect on the entire complex. “Continuous balconies radiate heat. To prevent this we used thermal breaks to reduce thermal bridging. Maas estimates that the project team installed more than 1,500 concrete-to-concrete thermal breaks, amounting to some 1,745 linear m (5,725 linear feet) to thermally break the balconies and to meet the NECB.
Project structural engineer, DIALOG’s Steven Oosterhof, notes, “Thermal breaks were proposed as a solution to thermal bridging and were carried through value engineering because of the value they bring. They are an excellent solution because they fully integrate into the structure. Working with the supplier, we were able to achieve acceptable strength and deflection performance of the cantilevered balcony structure.”
Schöck North America supplied the project with Isokorb® concrete-to-concrete load-bearing thermal breaks that insulate the balconies while also upholding their structural integrity. The modules consist of upper tension and bent shear reinforcement bars that penetrate a block of rigid insulation and are tied into the rebar of the floor slab and the balcony slab prior to pouring the concrete. The insulation block is 98 percent less conductive than concrete, while the stainless steel of the reinforcement bars is about one-third as conductive as the carbon steel rebar of the slab and the balcony, reducing heat loss at the penetrations by up to 90%. In addition to saving energy, the structural thermal breaks prevent interior surfaces adjacent to the penetration from chilling to dew point, forming condensation and supporting mould growth, while increasing interior floor temperatures opposite balcony slabs by up to 19°C (34°F) compared to a continuous floor slab.
Preliminary modeling from Footprint showed the structural thermal breaks saved 35,977 kWh for the entire development.
Oosterhof appreciates their function. “I have seen frost on the pony wall adjacent to a balcony when thermal breaks haven’t been used. Finishes are also susceptible to moisture because once cold air comes in through a thermal bridge, you’re going to get drywall wet, baseboards wet, etc. In the long term, mould can become an issue. And of course, there’s the thermal comfort that thermal breaks create. We’re the northernmost city of over one million people in North America. Our winter temperatures are often between -10 and -20° Celsius (14 and -4° F), and our coldest temperatures can dip below -40° Celsius (-40° F). So, thermal breaks are more important here. Yet surprisingly, only a couple of high-rise buildings in this market have used them.”
Maas adds, “Concrete balcony or slab extensions in cold weather will radiate cold into the suite. This is my second use of thermal breaks, but my first use of them for balconies. With advancing energy codes and continual use of concrete balconies, thermal breaks will become the norm very soon.”
A Thermal Break in the Action
Despite the project team’s enthusiasm for thermal breaks, some members had little experience designing with them. Naturally, unfamiliarity presented a slight challenge at the outset in terms of installation.
All stakeholders credit effective communication and professionalism for a fast learning curve on installing the thermal breaks. Oosterhof also cites a close working relationship with Schöck, the thermal break supplier.
“The process gave me confidence in the structural performance being consistent with what we needed as the structural engineer of record. We met with Schöck throughout design and construction, as a lot of coordination needs to happen so you don’t get reinforcement congestion issues onsite or constructability issues. To accomplish this, you have to involve the general contractor, the rebar placers, the concrete team, and the supplier.”
Oosterhof reports that the project team first created a mockup on site to make sure that everything fit together properly and that the installation sequence worked. Once approved and communicated, the process then became standard, taking advantage of the building’s mostly symmetrical floorplate. “We repeated this hundreds of times through the building.”
A Sister Building with a Key Difference
While outdoor space is required for high-rise residential buildings in Edmonton, that’s not the case for The Laurent student accommodation. Still, Diamond Schmitt integrated a rooftop lounge, among amenities like a fitness facility, study rooms and common rooms filled with natural light in a thoughtful design to support students’ health and well-being.
One of the largest student housing projects in Canada in the past decade, The Laurent provides 493 beds in 175 student residences occupying 17,466 sq m (188,000 sq ft) of space. Designed to protect against harsh winter temperatures, The Laurent has a well-insulated building envelope with opaque walls achieving an R value of 19 as well. All opaque sections feature rainscreen walls with five inches of exterior mineral wool insulation. The envelope also uses an energy efficient, double-glazed window-wall system, and terra cotta cladding attached via thermally broken clips. A heat recovery system captures heat and recycles it back into the tower mechanical systems.
Bowden adds, “It’s a good performing envelope and it adheres to Canada’s stringent National Energy Code for Buildings. Those same energy model requirements drove The Eleanor tower design as well to incorporate structural thermal breaks because of its balconies.”
Long-Term Plan
Maclab President and CEO Bill Blais began acquiring the property for The Laurent/Eleanor complex in the 1960s. “The area is attractive for a number of reasons. It’s anchored by the University of Alberta, and across the street is the University of Alberta Hospital, which is one of the strongest employment generators in Edmonton.”
Imbuing the project team with his long-term investment philosophy, Blais integrated his thinking into every aspect of the project, from amenities to efficiency and comfort. “Thermal breaks for the balconies serve as a perfect illustration, as they ensure resident comfort, provide energy/cost savings, and prevent condensation and potentially mould.” Accepting that thermal breaks come with an upfront cost, Bowden confirms the investment case: “It’s a cost that delivers a real benefit.”
Maclab Development Group
Diamond Schmitt
DIALOG
RDH Building Science
Ledcor Construction
Footprint
2024